Enhancing Your Welding WPS: Methods for Improved Performance and Efficiency
Enhancing Your Welding WPS: Methods for Improved Performance and Efficiency
Blog Article
Unlocking the Power of Welding WPS: Approaches for Effectiveness and Safety in Construction
In the world of construction, Welding Procedure Specs (WPS) stand as the foundation of welding operations, determining the needed actions for accomplishing both effectiveness and safety in the fabrication procedure. Understanding the complexities of WPS is critical to harnessing its full potential, yet several organizations battle to open truth power that lies within these files (welding WPS). By diving into the techniques that optimize welding WPS, a globe of boosted efficiency and increased safety and security awaits those going to discover the subtleties of this crucial aspect of fabrication

Relevance of Welding WPS
The importance of Welding Procedure Requirements (WPS) in the manufacture market can not be overemphasized. WPS act as a vital roadmap that lays out the essential steps to ensure welds are performed constantly and correctly. By specifying vital parameters such as welding procedures, products, joint layouts, preheat temperatures, interpass temperatures, filler steels, and post-weld heat therapy demands, WPS supply a standardized strategy to welding that improves performance, high quality, and safety and security in construction processes.
Adherence to WPS aids in achieving uniformity in weld high quality, reducing the probability of problems or architectural failures. This standardization likewise promotes conformity with industry regulations and codes, ensuring that fabricated structures satisfy the needed safety standards. In addition, WPS documentation enables welders to reproduce successful welding treatments, leading to regular results across various projects.
Fundamentally, the meticulous growth and stringent adherence to Welding Treatment Requirements are vital for upholding the stability of bonded frameworks, safeguarding against prospective threats, and upholding the credibility of fabrication business for providing high-quality product or services.
Crucial Element of Welding WPS
Enhancing Effectiveness With WPS
When optimizing welding operations, leveraging the essential elements described in Welding Procedure Specifications (WPS) becomes important for streamlining processes and making the most of productivity. One method to boost effectiveness with WPS is by meticulously choosing the ideal welding parameters. By sticking to the specific guidelines supplied in the WPS, welders can ensure that the welding devices is established correctly, causing high-quality and consistent welds. Furthermore, adhering to the pre-approved welding sequences detailed in the WPS can substantially lower the moment spent on each weld, eventually raising overall efficiency.
Frequently assessing and updating the WPS to integrate any kind of lessons learned or technological improvements can also contribute to performance enhancements in welding procedures. By accepting the guidelines established forth in the WPS and constantly looking for methods to optimize procedures, makers can accomplish higher performance levels and exceptional end results.
Ensuring Security in Manufacture

Security protocols in fabrication play a pivotal duty in guarding workers and enhancing functional treatments. Making sure security in construction involves a multifaceted approach that encompasses various elements of the welding process. check here One essential aspect is the stipulation of individual protective equipment (PPE) customized to the certain risks existing in the construction atmosphere. Welders should be geared up with appropriate equipment such as safety helmets, handwear covers, and safety garments to alleviate dangers connected with welding activities.
Furthermore, adherence to proper ventilation and fume extraction systems is crucial in preserving a healthy job environment. Welding fumes contain hazardous compounds that, if breathed in, can pose severe health dangers. Applying effective air flow steps aids to reduce direct exposure to these hazardous fumes, promoting respiratory system health among employees.
Regular devices upkeep and inspections are also necessary for ensuring safety and security in fabrication. Damaged equipment can web link bring about injuries and crashes, highlighting the relevance of routine checks and prompt repair services. By focusing on security actions and fostering a society of recognition, fabrication facilities can create a efficient and safe and secure job environment for their personnel.
Executing WPS Finest Practices
To improve functional performance and guarantee high quality end results in manufacture procedures, integrating Welding Treatment Requirements (WPS) best practices is critical - welding WPS. Carrying out WPS ideal techniques involves meticulous planning, adherence to market requirements, and constant tracking to guarantee optimal results. Firstly, picking the ideal welding procedure, filler product, and preheat temperature defined in the WPS is crucial for attaining the wanted weld top quality. Second of all, guaranteeing that qualified welders with the necessary certifications lug out the welding procedures according to the WPS standards is crucial for consistency and dependability. Routinely upgrading and evaluating WPS documents to mirror any kind of process improvements or adjustments in products is also a crucial ideal method to maintain precision and significance. Additionally, giving extensive training to welding personnel on WPS requirements and ideal methods fosters a culture of safety and security and find more information high quality within the construction environment. By faithfully carrying out WPS best techniques, fabricators can streamline their procedures, reduce mistakes, and provide exceptional products to meet client expectations.
Final Thought
In final thought, welding WPS plays a crucial role in guaranteeing effectiveness and security in fabrication procedures. By complying with these strategies, organizations can open the full potential of welding WPS in their fabrication operations.
In the realm of fabrication, Welding Procedure Specifications (WPS) stand as the backbone of welding procedures, determining the needed actions for attaining both performance and safety in the construction procedure. By specifying crucial parameters such as welding procedures, products, joint layouts, preheat temperature levels, interpass temperatures, filler metals, and post-weld heat therapy needs, WPS supply a standard method to welding that enhances efficiency, quality, and safety and security in manufacture processes.
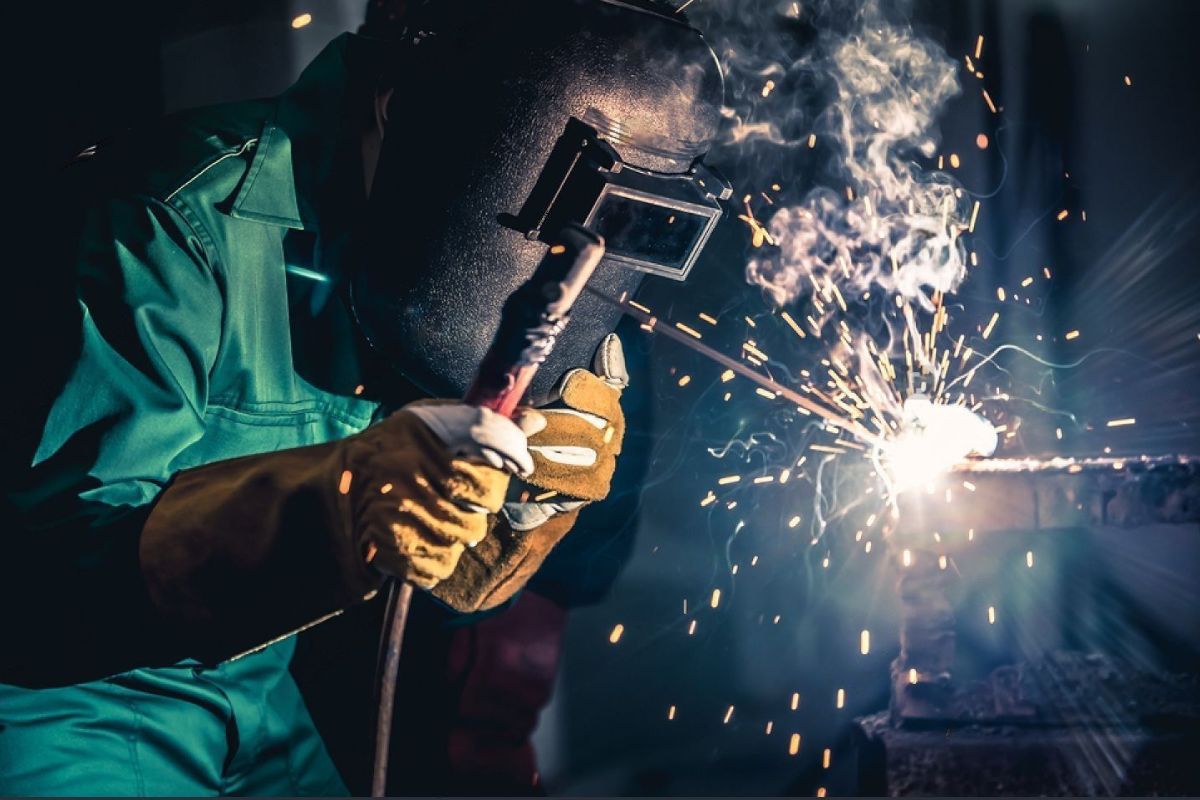
When maximizing welding operations, leveraging the essential components outlined in Welding Procedure Specs (WPS) comes to be important for enhancing procedures and maximizing efficiency. (welding WPS)
Report this page